Holding brakes, predictive diagnostics, and operational continuity: why intelligent control of mechanical safety is now a fundamental requirement in packaging systems – and how high-quality solutions like Mayr’s ROBA-brake checker can make the difference.
A constantly evolving market
The industrial packaging sector is one of the most dynamic areas of automation. According to the latest UCIMA report, Italy ranks among the world’s top producers of packaging machinery, with exports accounting for over 75% of production. The demand for fast, flexible, and safe systems continues to grow, driven by requirements for a wide range of formats, materials, and hygiene standards. In this highly competitive and technological context, the choice of components plays a strategic role in determining system reliability and availability.
A key element for safety
Among the components critical to machine safety, holding brakes play a crucial role. In many packaging systems – such as vertical form-fill-seal machines (VFFS), palletizers, pick-and-place units or case erectors – brakes are installed on vertical or inclined axes to hold mobile assemblies, dosing heads, handling modules or loading units in position. During scheduled stops or emergency shutdowns, the brake prevents uncontrolled movement or accidental falls.
What happens if the brake fails?
A brake failure can have serious consequences: falling components, damage to the line, packaging defects, or complete system shutdown. In extreme cases, it may also pose a safety hazard to operators. Like any mechanical device, brakes are subject to wear, contamination from dust or lubricants, and a gradual loss of braking capacity. Without continuous monitoring, degradation may go unnoticed until the moment of failure.
Tighter regulations and rising expectations
The push for intelligent, connected, and safe equipment also stems from regulatory requirements: the Machinery Directive 2006/42/EC, ISO 13849, and the increasingly strict specifications of major end users require active monitoring of safety-relevant components. Brakes used for position holding clearly fall into this category. Monitoring their condition is not just a technical decision – it’s a practical response to today’s market demands.
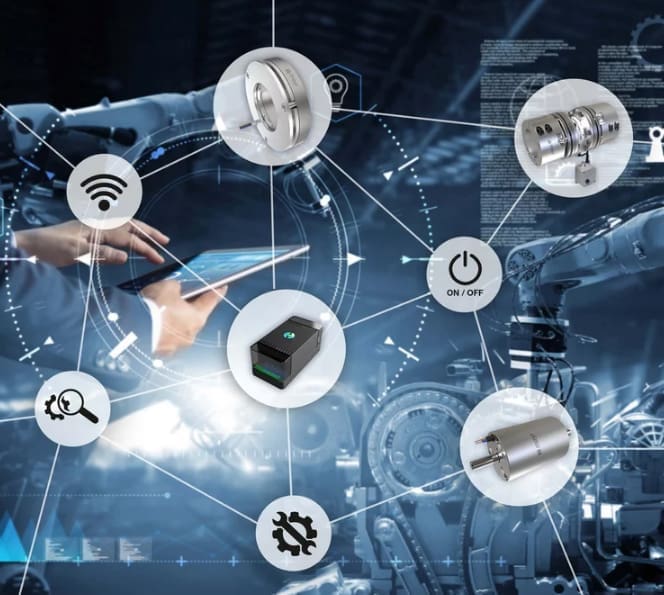
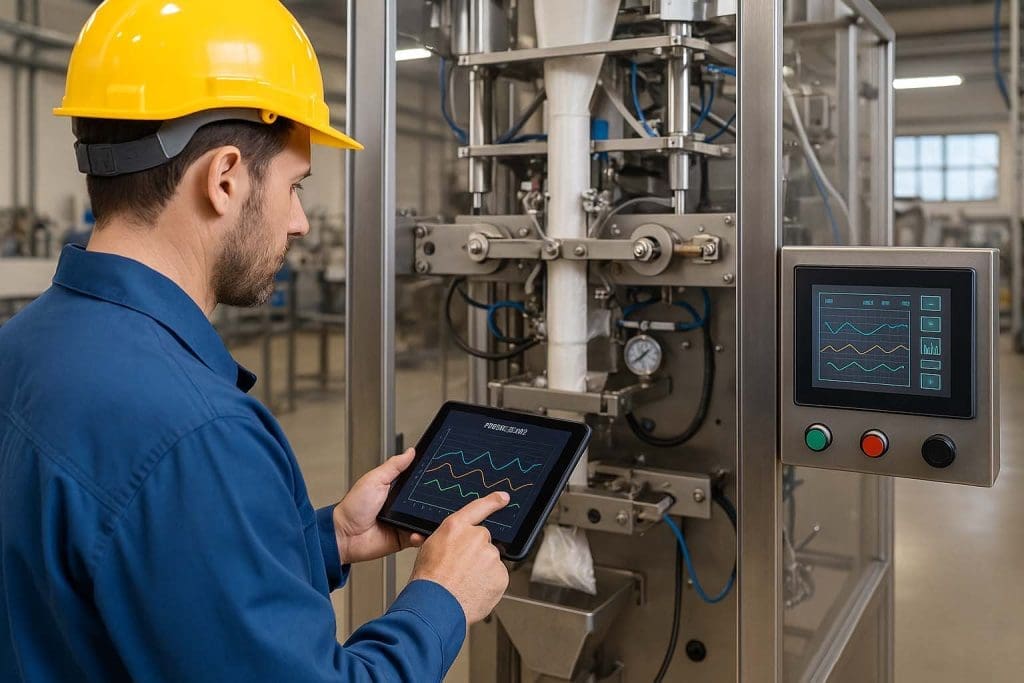
ROBA-brake checker: smart diagnostics with no extra sensors
To prevent unplanned downtime and ensure the safety of packaging lines, Mayr offers the ROBA-brake checker, an advanced electronic module that continuously monitors the condition of electromagnetic brakes – with no need for additional sensors or structural modifications to the machine. ROBA-brake checker analyzes the brake’s electrical parameters in real time – current, voltage, resistance, and temperature – and detects any anomalies related to wear, overheating, or malfunctions. When irregularities occur, it sends a warning signal in advance, allowing maintenance to be planned before a failure happens.
Predictive maintenance for improved efficiency
In modern packaging lines, every minute of unplanned downtime means lost productivity. Predictive maintenance allows intervention only when truly necessary, based on real-time data, optimizing maintenance resources and ensuring greater system availability. ROBA-brake checker aligns perfectly with Industry 4.0 strategies, helping to make the system safer, more reliable, and smarter.
Traditional vs. smart maintenance: the difference is clear
In a conventional brake, wear on the friction surfaces and spring fatigue can go undetected for a long time. The component may still function, but it progressively loses effectiveness until it no longer delivers the required braking capacity. Only a manual inspection – which may not always be performed – can reveal the issue.
A typical scenario: an avoidable accident
Imagine a vertical packaging machine where the dosing unit is held in place by a worn-out brake. During a film change or production pause, the motor stops, but the brake can no longer hold the load. The assembly drops suddenly, damaging the mechanism below and halting the process. The downtime lasts hours. If the degradation had been detected earlier, the brake could have been replaced during a scheduled maintenance window. Situations like this clearly show the value of ROBA-brake checker.

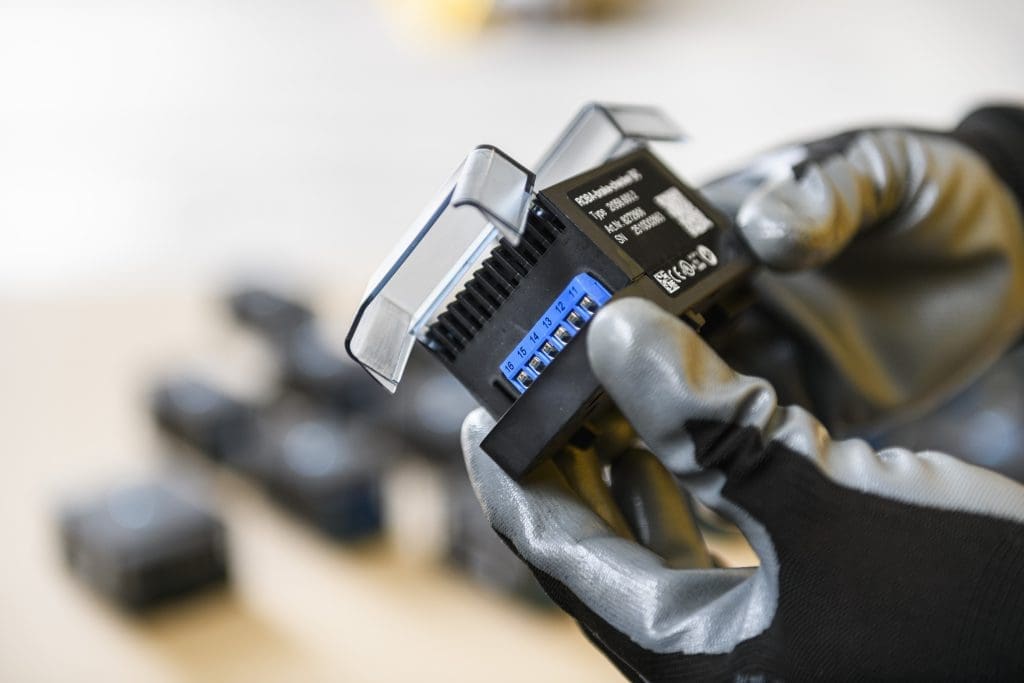
A technology ready for packaging lines
Compatible with a wide range of Mayr brakes – including the ROBA-stop-M series – and easily retrofittable on existing systems, ROBA-brake checker is designed to communicate with machine controls and support predictive maintenance strategies. Thanks to advanced logistics and a well-stocked local warehouse, Mayr Italia can ensure immediate availability and extremely fast delivery, even in case of urgent requests. In a sector where safety, precision, and operational continuity are key, investing in intelligent monitoring systems is a strategic decision. Choosing ROBA-brake checker means ensuring production uptime, reducing maintenance costs, and increasing overall system safety.
Since 1897, Mayr has been the trusted partner for drive and power transmission technologies, delivering innovative solutions to leading companies across a wide range of industries.
With its complete range of torque limiters, shaft couplings and safety brakes, the company can respond quickly to most customer requirements – thanks also to efficient logistics developed over decades of experience on the Italian market. The 400-square-meter warehouse in Italy allows Mayr to deliver the most requested products from stock.
Mayr’s technical specialists are available to provide free consulting to help identify the most suitable product – or to develop a custom solution within the customer’s production timeframe. For further information about Mayr solutions, contact the company by phone at +39 049 8791020, by email (info@mayr-italia.it), or visit mayr.com/en.