FuturaPack, a Gampack Group Company, creates an innovative robotic packaging line for a Global Key Account American multinational, world leader in baby food.
The baby food market has continued to expand and grow even in times of pandemic. Neither the effect of prolonged lockdowns nor the continuous decline in birth-rate have dampened the demand for this increasingly technological and specialized sector, where brand reputation is closely linked to a sense of responsibility towards the target audience.
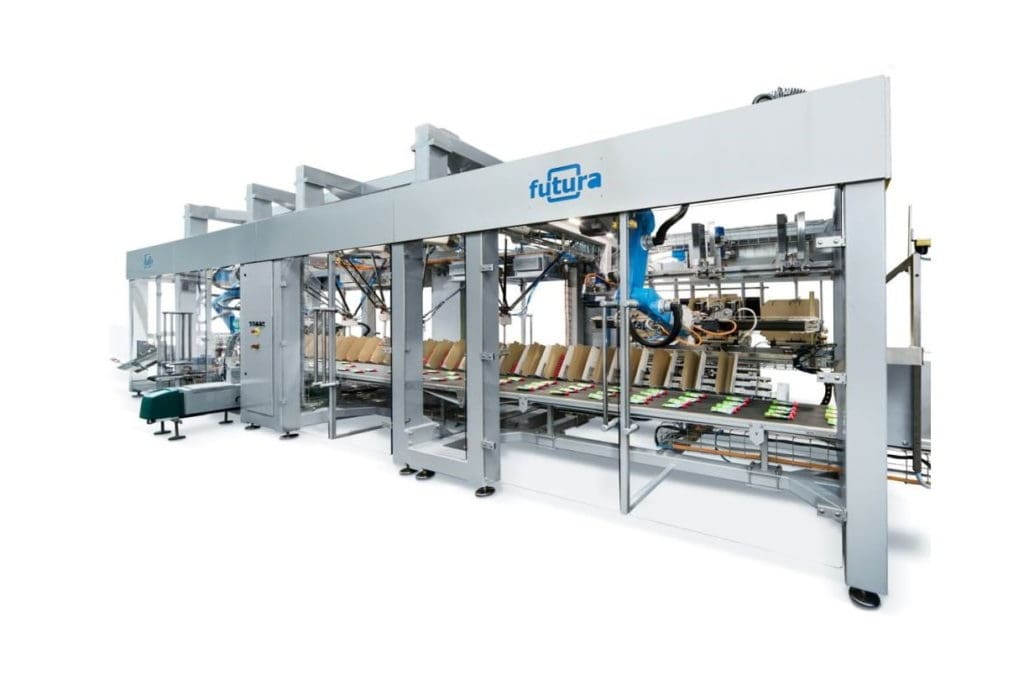
FuturaPack, a Gampack Group Company, based in Piacenza in the heart of the Emilian packaging valley, has specialized in end-of-line and robotic high-tech secondary packaging solutions in the food and beverage sector for many years.
Thanks to network synergy and simultaneous development in product innovation and an eco-sustainable packaging policy, FuturaPack has been able to counterbalance the crisis period by capitalizing on its core assets and utilizing the flexibility of its machines in order to respond to today’s very demanding market.
FuturaPack is already internationally renowned for its high-performance end-of-line systems, with many successful installations at production sites of major brands and co packers in a large variety of sectors, including food, dairy, beverage, pharmaceutical, cosmetics, home, and personal care around the world.
FuturaPack has had considerable success in the United States baby food market since its debut several years ago, delivering complete robotic lines for packaging cups containing fruit puree for children) Furthermore, the company’s business in this specific market segment concerning packaging technologies for baby food, has expanded, and has led to the design of even more sophisticated solutions in terms of engineering and design, thank to the latest generation robots manipulating doypack.
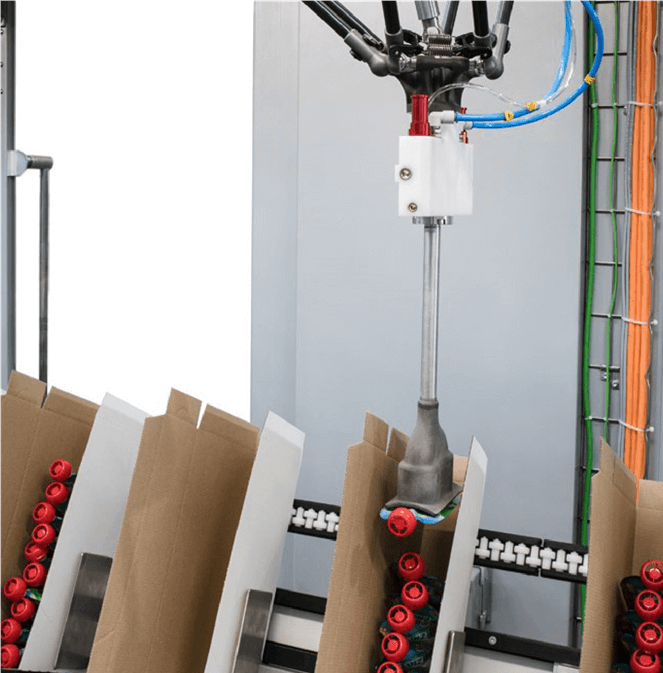
R&D in baby food technology have led to an important collaboration with an international company in the food and beverage market. The synergy between the companies has resulted in the development of many successful projects with high customer satisfaction through professional project management and an increasing operational interest at Customer sites.
In relation to this, a first robotic line for packaging baby food was installed at an important American international company in 2019.
Thanks to the success of this installation, the Customer confirmed his confidence and commissioned a second line, which will be delivered in the coming months. The robotic system designed and engineered by FuturaPack offers high flexibility, while ensuring a high degree of efficiency.
Let’s have a closer look about how this end-of-line system works. Doypacks, loaded manually on a conveyor belt arrive randomly arranged in 4 rows at 180 pieces/min. Perfect alignment and accurate orientation of the products are not needed since they arrive from the customer’s production line and from manual loading.
This avoids the need for a complicated orientation system and difficult regulations, which can often cause stumbling blocks. This process simplification, with the aim of eliminating complicated systems of directing and grouping products, is the ideal technical solution for the Customer.
Products leaving the production/filling line moist, are dried by an air flow and a simple vision system identifies their position, “communicating” it to the collection robots. Due to the constant flow rate of the products, four high-speed Delta robots are mounted on the machine structure.
The cardboard boxes are formed starting from flat blanks handled three at a time by three axes manipulator, controlled and inserted into an inclined pocket transport.
This technique allows the robots to store the product horizontally into the cardboard box and during the transfer, taking advantage of the maximum handling speed. The filling is done from the upper side of the box, whose flaps are open until the format is completed.
Thanks to this efficient filling operation process, the maximum capacity of the secondary packaging is ensured. Once the box filling is completed, the flaps are closed, the lid is pulled down and glued; the cardboard box returns to a horizontal position, where it is weighed and labelled.
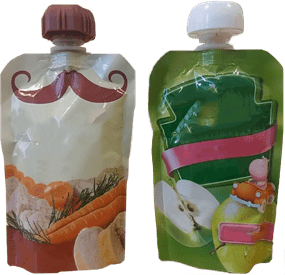
FuturaPack packaging machine can be equipped with an option of a static balance inside its frame to eject any incorrectly formed carton boxes and to only deliver the correct, controlled packages.
Thanks to the extensive knowledge gained during years of experience handling primary products (doypacks, envelopes, flowpacks…), FuturaPack has achieved several successes in the development and supply of packaging solutions at production sites of Various leading worldwide brands.
Futurapack has delivered during the years reliable, automated, and sustainable solutions, customized according to specific production needs.