Valley Water invests in a modern 36,000 bph PET plant
In the desert area of Wadi El Natrun, a depression about 23 meters below sea level, Elano water is extracted and bottled by the Valley Water company.
To increase the production of 0.6 L and 1.5 L PET bottles, the Egyptian company recently turned to SMI for the supply of a complete line of 36,000 bottles/hour, which is currently the most modern plant installed by SMI within the African continent and is the ideal solution to ensure efficient, sustainable and high-quality production.
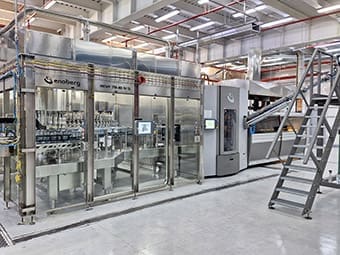
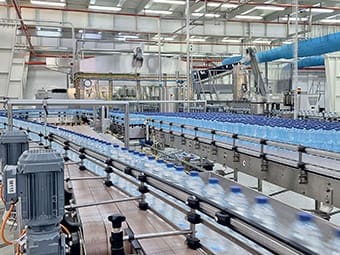
Investing in new technologies to increase efficiency and productivity
To preserve the quality of Elano water and offer consumers a pure, uncontaminated and healthy product, Valley Water pays great attention to every detail and, collaborating with the experts of the industry, invests in cutting-edge technologies, such as the recent bottling and packaging system supplied by SMI.
The decision to rely on SMI for the supply of a new complete line of 36,000 bottles/hour for the bottling and packaging of Elano water in PET bottles ranging from 0.6 to 1.5 L is the result of a close collaboration between the two companies, that began in 2013 with the installation of a rotary stretch-blow moulder and a shrink wrapper from the LSK range for the packaging of 0.33 / 0.5 / 1.5 L containers in PET.
SMI has also been involved in the process of automation of the end of the line of the pre-existing plant, to allow Valley Water to meet the growing demand for bottled water in Egypt, a market featuring one of the highest levels of consumption per capita in the world and in which consumers tend to choose healthy drinks. The new technologies supplied by SMI allow the company to achieve greater production capacity and efficiency, improved market competitiveness, high energy savings and reduced environmental impact.
Restyling of the bottles to improve performance
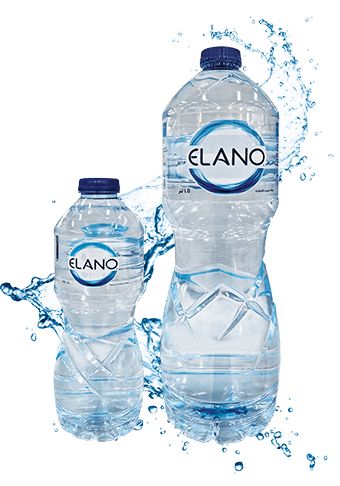
SMI has made the know-how acquired in the design of PET containers available to the customer.
Starting from existing 0.6 L and 1.5 L containers and keeping the “core concept” unchanged, SMI’s designers emphasized the iconic image represented and improved the resistance and stability of the containers. These objectives have been achieved by enlarging the maximum diameter of the bottles and lowering their height, with the result of optimizing the center of gravity of the same. The base of the bottle was also subject to a restyling process, with the aim of improving the mechanical properties of the containers during filling. Thanks to these measures and the supply of new moulds for the stretch-blowing, the entire packaging and palletizing process of Valley Water has become more efficient and sustainable.
SMI solutions for Valley Water
Valley Water pays great attention to environmental issues and for the bottling of Elano water in eco-compatible and recyclable PET bottles, uses green technologies of the latest generation that allow reduced environmental impact and significant energy savings. The 36,000 bottles/hour complete line supplied by SMI allows the customer to optimize the space within the production plant to have an efficient and performing line, able to meet the growing demands of the Egyptian market for a high quality product. The new system consists of an EBS 16 E ERGON stretch-blow moulder in ECOBLOC® version with a HEVF filling and capping system; a WP 600 ERGON case packer; an APS 3070 L ERGON palletizer; conveyor belts, labelling machine, encoder and control systems.

Main advantages
ECOBLOC® ERGON HEVF BLOWING-FILLING-CAPPING SYSTEM:
• compact solution for the blowing and filling of 0.6 L and 1.5 L PET containers: rinsing machine and air conveyors between the blower and the filler are not required
• reduced energy consumption
• high-efficiency rotary stretch-blow moulding system equipped with motorized stretch rods, for productions up to 36,000 bottles/hour
• precise management of the stretch rod stroke and accurate control of its position, as well as significant energy saving
• preform heating module with energy-efficient IR lamps
• two-stage air recovery system, which enables to reduce energy costs
• easy management of the format changeover
• filling system with high-precision flow meters installed near each tap
• walk-in frame to easily access the filler and capper
• filling chamber completely isolated from transmissions that do not come into contact with any type of liquid
• the machine frame is inclined towards the drainage points resulting in a higher level of hygiene
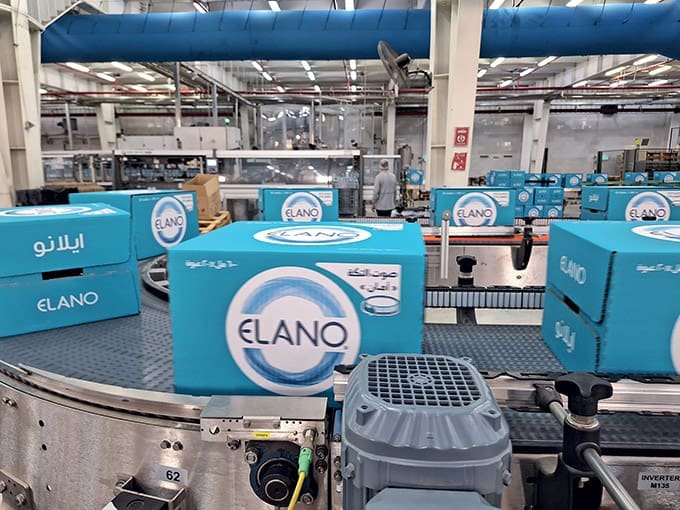
WP 600 ERGON WRAP-AROUND CASE PACKER:
• continuous packaging through a wrap-around system: smooth production process, without jerky movements
• ideal solution for packaging in impact-resistant 4×5 cases (0.6 bottles) and 3×4 cases (1.5 L bottles): higher protection of the product during transport
• better pack quality and reduced mechanical wear
• possibility to graphically customize the cardboard box
• extremely ergonomic machine structure
• easy and safe maintenance operations
• sliding POSYC® control panel, which allows the operator an easy and efficient use of the system
• highly intuitive, graphical interface, touch-sensitive screen and advanced real-time diagnostics and technical support.
APS 3070 L ERGON AUTOMATIC PALLETIZING SYSTEM
• single-column system with two Cartesian axes for palletizing cardboard boxes arriving from the WP 600 ERGON in 1000×1200 mm pallets
• extremely flexible modular structure, easily adaptable to the logistical conditions of the line
• ergonomic system that allows the operator to easily and safely carry out all activities related to the use, cleaning and maintenance of the system
• high operational flexibility that allows the creation of multiple palletizing patterns
• eco-sustainable solution, thanks to the use of ICOS motors equipped with integrated digital servo-drive (driver), able to simplify the wiring of the machine and ensure greater energy efficiency, lower noise and reduced wear of the components
• optimized TCO (Total Cost of Ownership) thanks to low management and maintenance costs.