SMI designs and manufactures bottling and packaging machines with an innovative design, equipped with IoT technology, in order to supply smart solutions for meeting the needs of competitiveness, production efficiency, flexibility, energy saving and easy management of the whole production plant.
The companies that operate in the food and beverage sector must in fact have a strong business competitiveness and be able to quickly adapt their production lines to the new market requirements.
The answer to these needs lies in choosing bottling and packaging machines and systems that are compact, flexible and environmental sustainable, designed for the smart factory and equipped with cutting-edge automation and control systems inspired to Industry 4.0 and Internet of Things (IoT) principles.

Packaging plays an increasingly essential role and for every company it is fundamental to provide large retailers with practical, resistant and eye-catching packs. Among the latest developments in the packaging industry, resulting from continuous investments in new products and technologies, aimed at providing the users with an appropriate support to face the market challenges, there is the new ASW 30 T ERGON shrink wrapper with single lane infeed and 90° product infeed and the latest APS 615 ERGON semi-automatic palletizer.
The combination of these two machines offers all the advantages of an extremely compact, flexible and efficient end of line, that allows the food and beverage companies to easily adapt the production according to the changing consumption habits.
Compact ASW ERGON shrink wrapper with 90° infeed
In order to automate and optimize the end-of-line secondary packaging process, SMI offers different solutions suitable for every packaging need: from packs in film only, with cardboard pad or tray, to cardboard boxes, to multipacks in overlapping sleeves, etc.
For SMI investments in cutting-edge technology and innovation are the main driver for success in every company. Among the latest innovations in its product range, SMI has introduced 6 new models dedicated to the packaging of different containers with a cylindrical, oval or square/rectangular base at the maximum output of 30 (ASW 30) and 40 (ASW 40) packs per minute.
The advantages of ASW 30 T ERGON packer
– equipped with a single lane infeed, the ASW 30 T ERGON showcased at the trade fair offers the considerable advantage, also in economic terms, of not requiring the presence of a divider for channeling loose products
– the format changeover operations are quickly and easily performed, as it is possible to process various types of containers, of different sizes, without having to use any additional equipment
– compact solution that easily adapts to the logistical conditions of the end of line of any production plant
– the system with single lane infeed, preferably positioned on the side opposite to the operator, simplifies the correct channeling of loose products on a conveyor belt equipped with low friction thermoplastic chains
– in the pack formation area a pneumatic device groups the containers alternately before the packaging operation in the desired configuration; this section is characterized by a double belt system, that, by means of an electronic cam, separates the product according to the format to be processed. Subsequently, thanks to a rotary feeder, loose products are moved from the single lane to the multi-lane conveyor at the machine infeed
– the cardboard magazine is positioned under the infeed conveyor; from here the corrugated cardboard pads or trays, taken by means of an alternating motion picker equipped with a group of suction cups with pneumatic vacuum system run along the cardboard ramp and are positioned under a group of incoming products with the long side leading
– the unwinding of the film reels, positioned in the lower part of the machines, is controlled by a progressive brake that ensures optimal film tensioning
– the film splicing at the end of the reel occurs by means of a manual sealing bar. The reel-holder spindles have pneumatic locking and when the film reel is running out, a special device stops the machine.
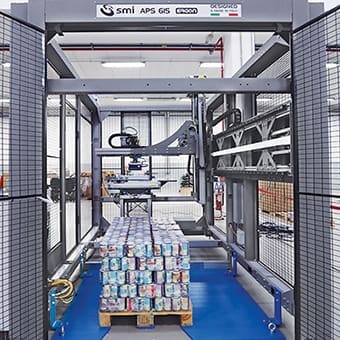
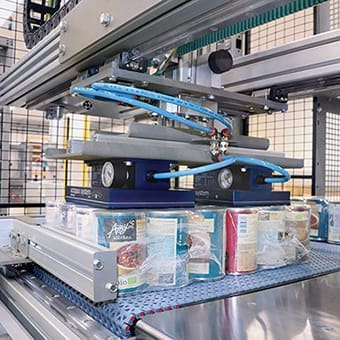
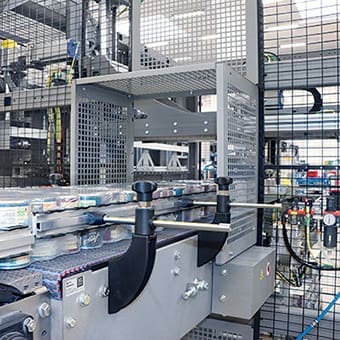
Compact APS 615 ERGON palletizer
The tertiary packaging of food requires increasingly flexible solutions for improving the handling of the containers and avoiding damages during their handling, reducing the format changeover time in order to quickly adapt the production to the new palletizing patterns and increase the performance with a reduced space.
APS 615 ERGON palletizing system stands out for:
– compact and ergonomic structure, that allows a significant space saving within low-speed bottling plants
– the ergonomic and functional structure of the APS ERGON allows the operator to easily and safely perform the activities related to installation, management and maintenance
– use of innovative, smart and customized technical solutions, that offer considerable advantages in terms of operational flexibility and economic competitiveness of the processes
– optimized TCO (Total Cost of Ownership) thanks to low operating and maintenance costs
– high level of flexibility, thanks to the possibility to realize several palletizing patterns, according to the specific customers’ needs
– use of cutting-edge technology, that ensures great operational flexibility and possibility to adapt to the needs of format changeover, product changeover and/or plant layout
– the operations are controlled by a user-friendly machine automation and control system, guaranteed by an extremely intuitive graphic interface, by a touchscreen display and by POSYC® real time diagnostics and technical support functions
– the electrical panel, positioned outside the safety guards is a different module, that is not unwired during the transport and can be immediately installed at the customer’s plant
Compact and functional structure
The core of the APS 615 ERGON semi-automatic palletizing system is composed of the structure where the three Cartesian axis system designed for the pallet formation is positioned. This is added to the infeed conveyor, the product picking head and the machine guards. At the palletizer infeed, the product arrives at the product feeding conveyor and is cadenced by the rubber conveyor.
Subsequently, it is brought into the picking position by a distancing conveyor; here the gripping head picks the pack, individually or grouped, and moves it to the pallet on the ground. The cyclic repetition of this operation enables to create several palletizing layers.
The picking head is equipped with a motor for the product rotation, in order to place the pack on the layer in the position required by the palletizing pattern. Once the pallet formation has finished, the operator manually removes the full pallet and positions a new empty pallet.
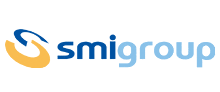