AlphaMAC was born at the beginning of 2019 as the brainchild of a group of highly specialized experts in the packaging fi ld who wanted to build an innovation driven company, which would stand out for its ability to adapt to the various needs of users and would create added value through its solutions for existing and newly emerging problems. Our team, has decades of experience in the fi ld of extrusion and blow-molding and an in-depth knowledge of the latest technologies, raw materials and complete packaging lines. This combination has helped us to become, within a very short period of time, a reference point in the industry for machinery for the production of plastic fl id containers. “Our lean production structure” Our business model is in itself not new and it has long been used in other segments of the packaging machinery manufacturing industry. What’s new is that it had never yet been applied to companies building extrusion and blow-molding machines. Our approach involves a focus inside the company on the different high value activities– activities such as the management and supervision of design activities, research and development of innovation, in particular with regard to new raw materials, sales and customer support.
The remaining so-called “low value” activities are delegated to a consolidated network of companies specialized in the construction and testing of automatic packaging machinery. Specificall , this group is made up of 32 companies that work closely with each other, all located within a geographically defin d area, which therefore allows a continuous and simple monitoring of operations. The synergy generated through this interaction between industrial partners – all of whom are highly specialized in their own sector of activity – results in a process that is extremely flexible, but with significantly lower fi ed costs and a high-quality standard. Moreover, this cooperative approach ensures that all partner companies are continuously updated on the new technological solutions being developed and applied in automatic machines, which in turn enhances the quality and effici ncy of our machinery.
“The latest trends in extrusion and blow-molding”
The use of fully electric machines is certainly one very important trend in the short and medium term. This is a partially consolidated technology, having been introduced to the market a decade ago. However, the rapid developments in technology and electronics still offers significant improvements to be made, which results can be for example a lower energy consumption of the machines and easier operation. To date, many converters and end users still have a significant number of hydraulic machines that will need to be replaced by more modern machines.
Another current trend is the use of highly flexible machines for various types of raw materials, in particular PCR (postconsumer resin) materials, as these are materials that will have to be used in much higher percentages in the future. Not all machines have extrusion screws suitable to maintain a stable process with these materials. In addition, there are the new bio-materials that are currently under development or being experimented with that will not only certainly reach the market in the coming years but will become a mandatory choice for bottle producers.
Machines today must offer the users the ability to change formats quickly so that production effici ncy and reconfig ration fl xibility for different applications are not impacted. They must be simple to use, with the latest generation of intuitive HMIs that allow dialogue and the monitoring of production data, offering reliable technical solutions that guarantee perfect operation for years at the lowest possible energy level and with maximum effici ncy.
www.alphamac.it
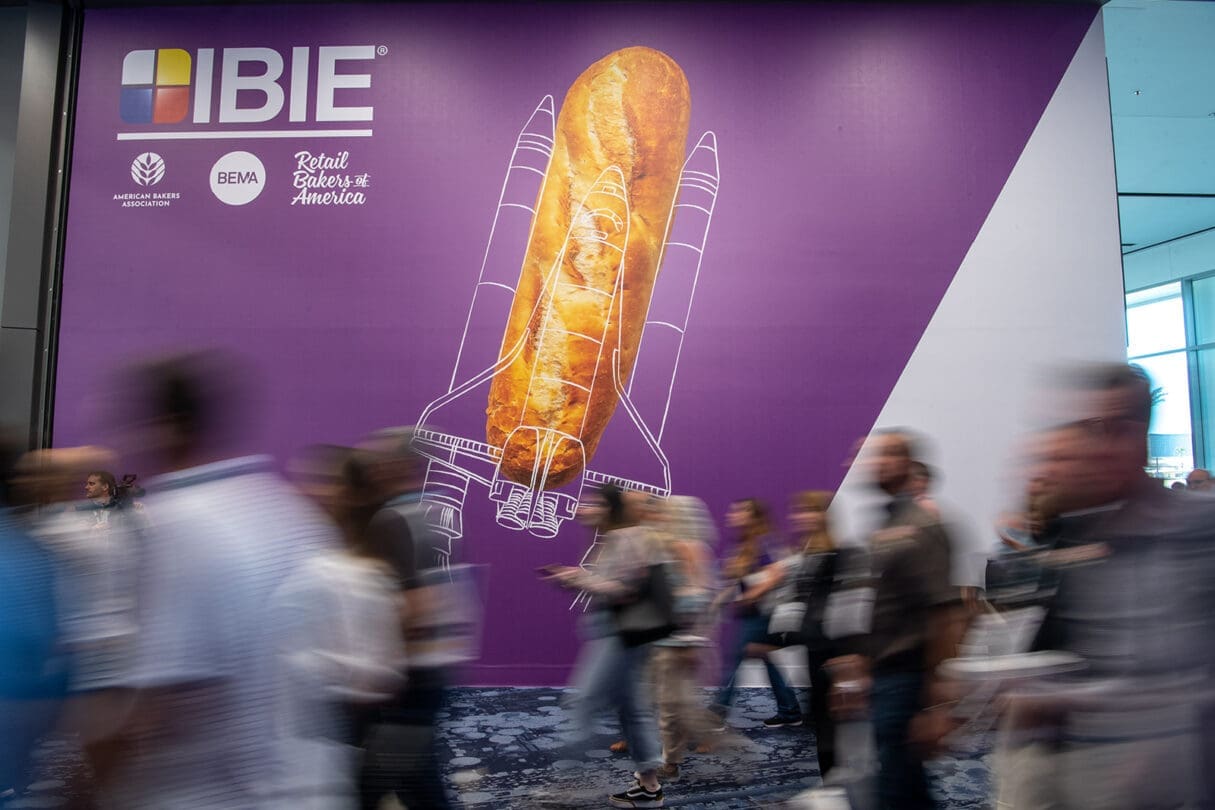
Unleash Your Baking Potential: IBIE 2025 – A World of Opportunities in Las Vegas
The international baking community is buzzing with anticipation for the International Baking