Thanks to the deployment of advanced technology coupled to optimised machine design, ZACMI’s filling and sealing solutions are setting the pace in the sauce market
Italian company ZACMI is an expert in helping its customers adapt, keep pace with and lead the market in terms of packaging formats and foodstuff variety. Nowhere is this more evident than in its filing technology, especially when it comes to sauces, both thick or thin and hot or cold, with or without inclusions, such as guacamole, chipotle sauce, mayonnaise, ketchup, purées and pastes. ZACMI offers a comprehensive range of filling solutions for these foods, for both glass and plastic containers.
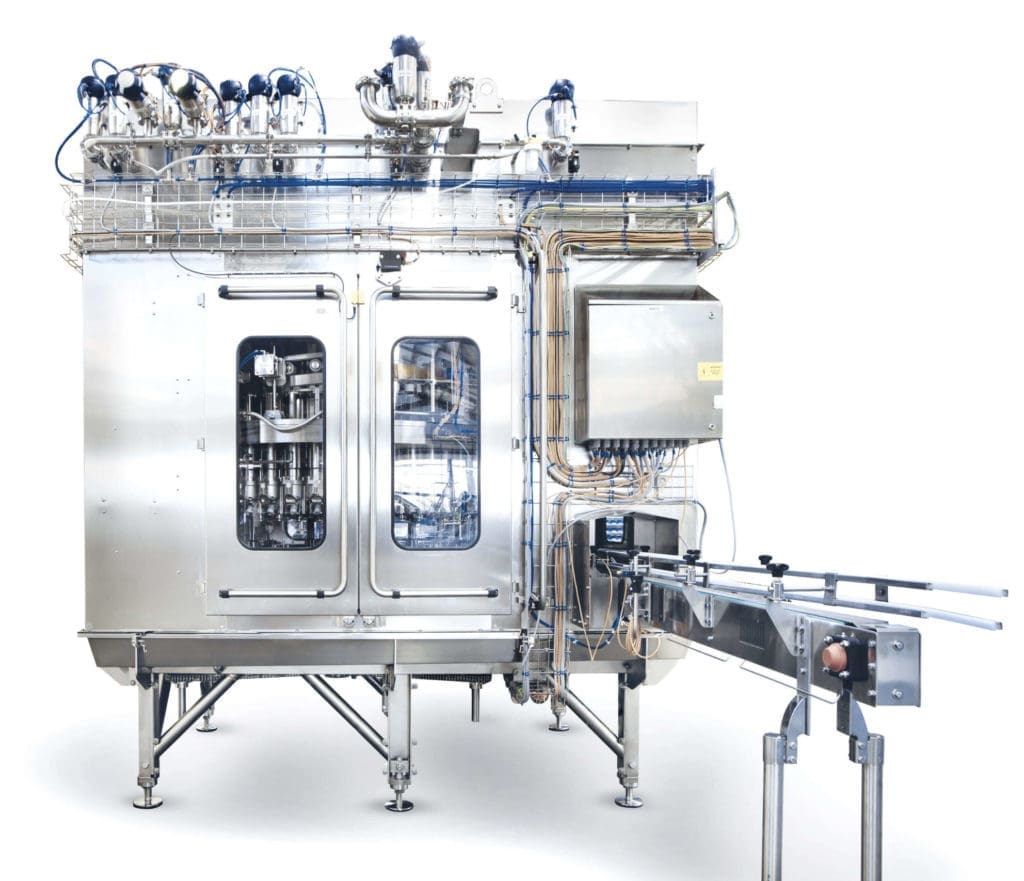
With multiple success across the globe, one of its most in-demand technology is its Piston Filler, which uses high levels of automation to maintain precise control over all process parameters. Further flexibility is delivered by the container in-feed screw, which can be independently driven and very tightly controlled using a servomotor. A special valve design prevents dripping, especially with oilbased sauces.
Although piston filling is a common technology, ZACMI has differentiated itself with the development of its patent ed Vertical Valve Piston Filler, which offers exceptionally high filling accuracy, making it suitable for a huge range of products, including Juice, dressing, sauces, marmalade, ketchup, mayonnaise, condensed/evaporated milk, edible oil, pet food, baby food & purée, soups, paté.
In-process cleanliness can be further assured with a cleanroom enclosure that offers tight contamination control, while a rapid CIP wash system keeps downtime to an absolute minimum by allowing quick and easy product changeover and this is backed by external WIP.
In parallel – on every cycle – the dosing system’s special software automatically measures the fill volume, the fill pressure and the fill time, compares these to optimum target values and then adjusts the next dosed value, minimising the standard deviation.
In addition to its impressive accuracy and throughput, the filling solution can handle a wide variety of container sizes without the need to change the valves and it has very low maintenance demands and costs.
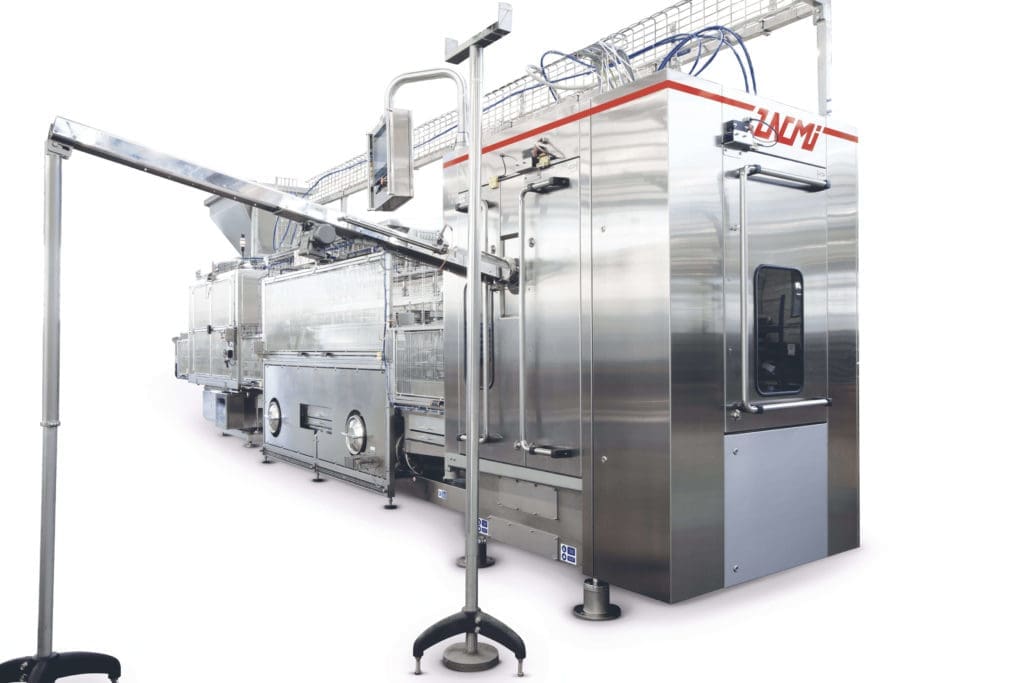
Customers can also connect with ZACMI’s Remote Assistance System, which is integral part of every machine – from Installation all the way through the machine’s life cycle. As well as monitoring and supporting troubleshooting activities, it can guide operators through HMI interaction and addressing software issues and upgrades without the need for a technician. The system boosts efficiency too, by reducing both start-up times and downtime.
For companies packaging into cans, Zacmi also offers its market-leading seaming solution. Controlled by a desmodromic cam, it is available in 3, 4, 6, 8, 10 or 12 multi-head configurations, delivering a maximum output of 1,600 cans per minute.
The company’s Double Seam Monitoring (DSM) solution checks the cans’ seaming performance in real time using special sensors. Its output can also be used for machine-settings regulation, ultimately helping to extend the service life of chucks and rolls.
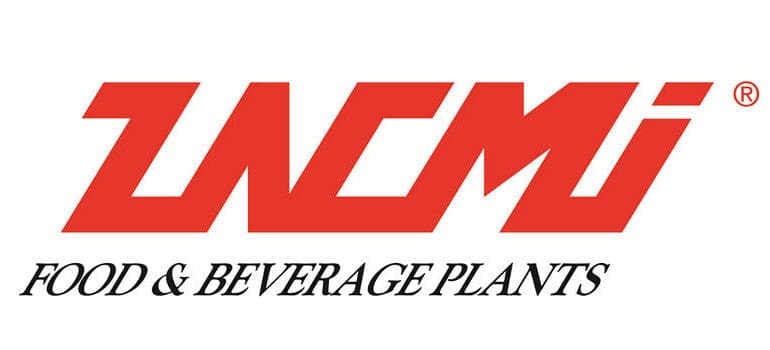