The industrial world in general, and the bottling and packaging sector in particular, is experiencing a rapid evolution triggered by the upheavals caused by the pandemic, which can be tackled efficiently and sustainably thanks to the advantages offered by digitization and automation.

SMI continuously invests in the development of packaging solutions, suitable to meet the needs of greater production efficiency and energy saving of production plants, offering a wide range of high-tech automatic machines capable of ensuring more flexibility, reliability and eco-sustainability.
In keeping with this goal, SMI has decided to renew the historic range of the SK series shrink film packaging machines, which, with the 2021 version, is enriched with new hi-tech solutions to improve the entire packaging process and reduce the costs of production and management of the plant.
Maximum levels of functionality with the innovative “Easy-load” magazine
The P and T models of the SK ERGON twin lane shrink-wrappers, suitable for processing pack formats in flat cardboard + film and tray + film, are fitted with the Easy-load device as standard, i.e. an automatic system for loading cardboard, consisting of a series of motorized belt conveyors dedicated to feeding the carton magazine on the packaging machine.
The advance of the cartons along the conveyor belts and their loading into the machine magazine, in order to optimize production efficiency, are managed by the automation and control system of the same. The Easy-load carton magazine is the ideal solution for packaging multiple types of containers in various pack formats, quickly passing from one configuration to another, because it ensures greater efficiency and precision in the management of dies of different thickness and guarantees greater tolerance in the variations of the same.
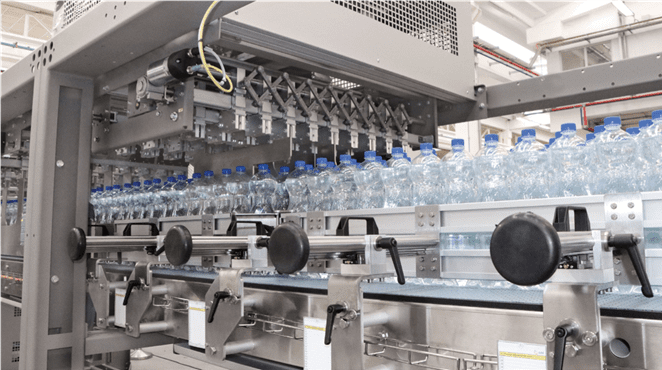
From an operational and functional point of view, the horizontal positioning of cardboard and the ergonomic design of the entire system allow the operator to easily load the stacks of blanks onto the magazine feed belts, placed externally to the machine at a working height congenial to this operation (instead of below it as in more traditional solutions).
By simply pressing a button, , the magazine automatically loads the stacks in the stripping area. The magazine is made up of modules, so it is possible to increase its autonomy by configuring more modules, to further simplify the work of the operator and optimize the production process to the maximum.
Motors with integrated digital servo drives
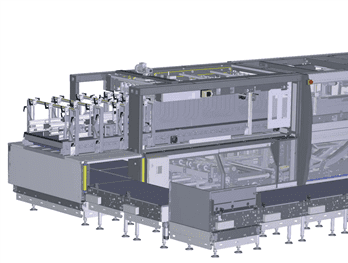
The new SK ERGON shrinkwrappers are fitted with Smitec ICOS motors equipped with integrated servo drives as standard, designed to guarantee high performance and remarkable results in terms of energy savings. Thanks to the distributed “DC share” architecture, these servo drives make it possible to exploit the energy generated by the motors during the deceleration phase, sharing it with the other devices installed on the packaging machine.
Optimized to meet demanding applications on modern machinery, the brushless servo motors with integrated inverter, installed on the SK shrinkwrappers offer extraordinary flexibility thanks to a rich set of on-board I / O, real-time fieldbus and sophisticated control algorithms.
They also represent a space-saving solution, thanks to the decentralization on the machine, which allows to reduce the size of the electrical panels and the relative air conditioning system. Furthermore, using a specific power supply, it is possible to connect up to 32 devices without the need for expensive shielded cables.
No maintenance thanks to self-lubricating chains
The new generation SK series of shrinkwrappers boasts an important innovation, which allows maintenance operations to be minimized, achieve maximum performance and eliminate the use of lubricants that could come into contact with the packed food product.
The new SK ERGON 2021, are fitted with special self-lubricating chains as standard, the particularity of which, is that they do not require the use of lubricant, which is necessary for standard chains, thus representing a long-lasting solution without maintenance.
This innovative solution offers two important advantages: on the one hand, it eliminates the danger of altering the packaged goods with the lubricant during their handling on the machine conveyor belt; on the other, it does not require the periodic maintenance required for classic chains, which consists of lubricating the chain links which are in continuous friction with each other.
Semplified format changeover
The latest generation SK ERGON series packaging machines are fitted with new sides on the infeed belt as standard, these are equipped with side guides with new rollers and profiles that vastly simplify format changeover activities, reducing the time required to switch from one pack configuration to another.
This solution is particularly useful for companies that need to process containers of different diameters, in different pack configurations, passing quickly and easily from one format to another and maintaining high production efficiency. The SK series can be equipped with special optional devices to further reduce format changeover times when the user has to switch from processing loose products to packaging pre-made bundles.
Intelligent data analysis
We cannot talk about the SK ERGON series without talking about the Smart Factory in general and Smart Production and Smart Service in particular. In a context where it is essential to continuously monitor and intelligently manage production, the choices adopted by SMI in terms of advanced automation and “IoT-embedded” applications play fundamental role in achieving the sustainable growth objectives of a wide audience of companies.
The new SK ERGONs have their own line supervisor to record, analyze, optimize, automatically modify the production and operating parameters, exchange data and information with other machines and systems within a bottling and packaging line, to carry out self-diagnostic activities to detect and solve faults or anomalies, to notify the operator of the need for ordinary or extraordinary maintenance and so on.
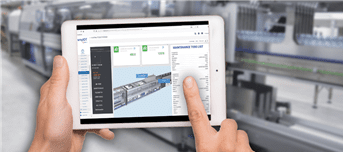
Thanks to this innovative system, companies of SMI customers can easily identify the main causes of downtime of the production line, obtain an improvement in the overall efficiency of the same and reduce the time for plant maintenance and format changes.
It is also possible to obtain a structured report to perform cross-functional analyzes.
Maintenance which is more and more predictive Today, in the era of Industry 4.0, in the business environment we hear, more and more often about predictive maintenance, which is added to the now consolidated, preventive maintenance.
Thanks to the digital intelligence they are equipped with, the latest generation SK ERGON shrinkwrappers can benefit from the SMYIOT platform developed by SMI for predictive maintenance, which has the task of constantly checking the health of the machinery in order to prevent breakdowns and malfunctions.
A modem and special software is all that is needed to manage the large amount of data, the so-called “Big Data”, collected by the sensors installed on the machines. This information then becomes the basic building blocks of the control and management system that oversees the improvement of the efficiency of the production plants, the reduction of the risks associated with a potential malfunction, the prevention of any downtimes and the reduction of maintenance costs.
SMYIOT is basically a powerful monitoring and analysis program that, through the intersection of data of different nature and origin, builds an input and output information model that allows to intervene on the plants, only when it is really necessary.
More specifically, the digital platform developed by SMI analyzes, archives and translates the operating data of the machines into information that is immediately accessible to the specialized technicians in charge of their management, who, thanks to special automatic alerts, are able to plan maintenance interventions on the production line based on the predictive analyzes generated by SMYIOT, replacing a certain component about to break before this event occurs.
