At Anuga Foodtec 2024, one of the most important international trade fairs for the food & beverage industry, SMI will be present and showcase its latest developments in the packaging industry, resulting from continuous investments in new technologies to provide users with solutions capable of quickly adapting the production processes to the new market requirements.
Food and beverage industry plays a relevant role in the global economy and at the same time has a strong responsibility towards the planet, especially in the global consumption of energy and water used in production processes. For this reason, it relies on suppliers’ innovative nature, to adopt strategies capable of ensuring a responsible use of resources.
Responsibility is actually the main topic of Anuga FoodTec 2024. SMI will show how the employment of innovative technologies can lead the food and beverage industry towards a path of an innovative nutrition system.
The end of line solution presented by SMI at booth C011 – Hall 7.1 includes the new APS 620 ERGON palletizer, an extremely compact, flexible and efficient system, that allows food and beverage manufacturers to easily adapt the production to changing market consumer habits.
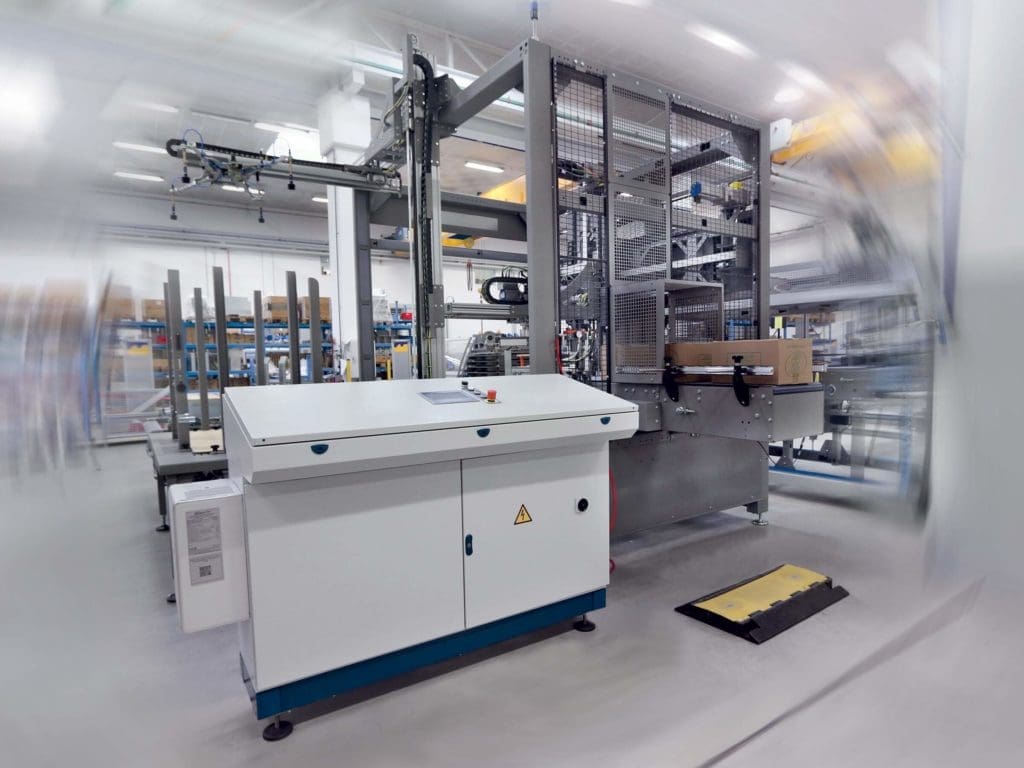
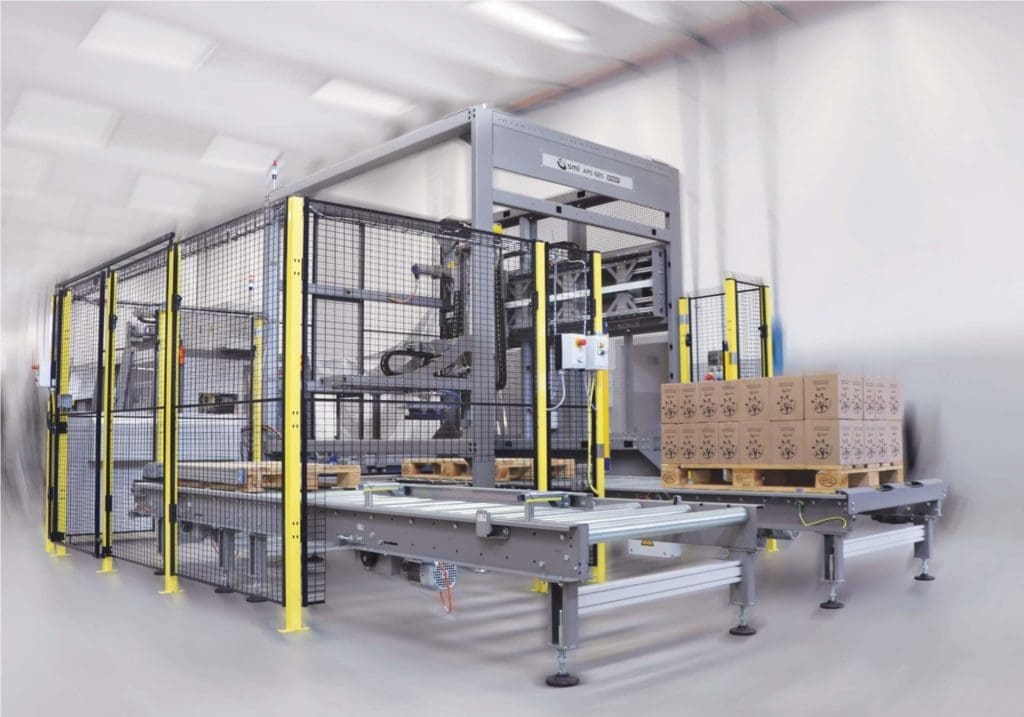
The displayed system will show the palletizing of small cardboard boxes containing 0.122 L PET spice jars packed in 3×4 format. The APS 620 automatic palletizer is suitable for medium-low production speeds up to 20 packs per minute (depending on the palletizing pattern).
The advantages of SMI palletizers
The tertiary packaging of food requires increasingly versatile solutions to improve the handling of containers and avoid damages during their transport, reduce the format changeover times to quickly adapt the production to new palletizing patterns and increase the performance with reduced dimensions.
SMI designs and produces bottling and packaging machines with an innovative design, equipped with IoT technology, to supply smart solutions that meet the requirements in terms of competitiveness, production efficiency, flexibility, energy saving and easy management of the whole production plant.
The use of an automatic palletizer is the ideal solution that ensures advantages in terms of productivity, costs, safety and quality, thus allowing companies to optimize logistic operations and improve the competitiveness on the market.
APS 620 ERGON: compact and functional structure
The core of the APS 620 ERGON automatic palletizing system is composed of the structure in which the three Cartesian axis system, performing the pallet formation, is positioned.

Added to this are the infeed conveyor, the product picking head and the machine guards. The product arrives at the palletizer on a product feeding conveyor and is cadenced by a rubberized conveyor. Later, it is brought into the picking position by a distancing conveyor, where the picking head lifts the pack, individually or grouped, and deposits it on the pallet on the ground.
The cyclical repetition of this operation enables to form several palletizing layers. The gripping head is equipped with a motor for the product rotation, in order to place the pack on the layer in the exact position required by the palletizing pattern.
Once the pallet formation is finished, the complete pallet is brought into the unloading area and, at the same time, at the infeed, in the formation area, a palletizing feeding system positions a new empty pallet, so that a new palletizing cycle can start.
MAIN FEATURES:
• compact and ergonomic structure, that ensures considerable space saving inside the production line;
• the ergonomic and functional structure of the APS ERGON allows the operator to easily and safely perform all the activities related to installation, management and maintenance;
• optimized TCO (Total Cost Ownership) thanks to low management and maintenance costs;
• use of technologies of the latest generation that ensure high operational versatility and customization possibilities to adapt to the needs of format changeover, product changeover and/or plant layout;
• the operations are controlled by a user-friendly machine automation and control system, thanks to an extremely intuitive graphic interface, the touchscreen display and the real-time diagnostic functions and technical support on POSYC®
•the electric panel, located outside the safety guards, represents a distinct module which remains cabled during transport and therefore can be immediately installed at the customer’s plant. ADVANTAGES:
• Higher production efficiency: APS 620 automatic palletizer works continuously and at a constant speed, thus increasing the productivity and reducing the endof-line operations. •Precision: palletizers are set for a precise positioning of the cardboard on the pallet, thus managing correctly the distribution of the load and preventing damages to products during the transport or storage operations.
• Greater safety for the operator: the automation of the operations managed by the palletizer reduces the risks connected to the movement of heavy loads on the end of the line
•Flexibility: the system easily manages different types of products, formats or palletizing patterns, ensuring significant advantages in terms of operational flexibility and economic advantages of productivity processes
•Space optimization: products positioned efficiently ensure the optimization of the space available on the pallet, thus reducing transport and storage costs.
