In 2018 there were in the European Union 136 alerts for dangerous foreign bodies (FBs) contained in the food products, with an increase of about 35% compared to the previous year.
This data is the reason why Xnext® was created to respond to the new industrial and commercial challenges of our time, introducing an extremely capillary and effective control system that saves companies time and money, and drastically reduces the number of products that are recalled from the market due to consumer complaints.
No matter how much care is taken in choosing healthy and organic food, no matter how much attention is given to the production chain, this initial data highlights how far there is still to go in the field of food inspection.
Given that the most frequent contaminant found in company analyses is plastic, which is highly harmful to the body and increasingly common in organic raw materials, new solutions to the problem are required, namely relying on more efficient methods using more detailed multilevel analysis.
Xnext® has developed the heart of its x-ray multi-energy system, XSpectra®, to further increase the quality of supply chain control.
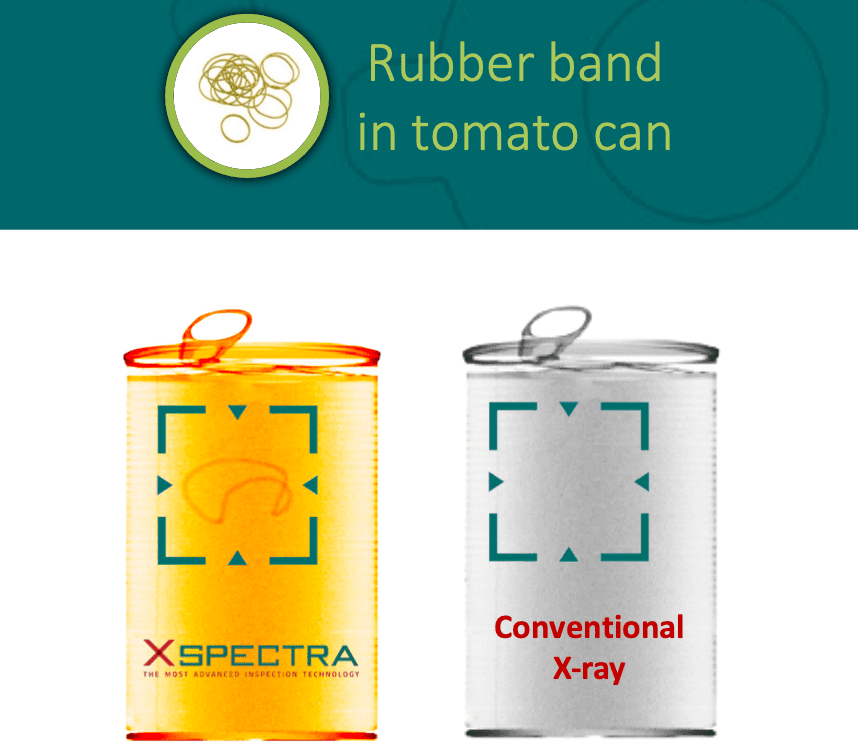

XSpectra® is based on inspection technology that is capable of detecting even very low-density foreign bodies and is designed to interact seamlessly with every production system currently on the market.
The inspection machine is usually inserted at the end of the production chain in order to find most contaminants at once, but can be inserted into all three main stages of the production chain, at the start with an analysis of the external contaminants of the raw materials, after the food components have been processed, and directly in the final inspection when the product has already been provided with its outer packaging, where a further analysis is carried out to assess the condition of the package and its final contents before being placed on pallets for shipment.
Analyses are carried out using a multilevel approach based on photonics and nuclear electronics, which are brought together using artificial intelligence algorithms.
This system is the result of 9 years of research and, compared with current inspection systems, allows very low energies (below 5 keV) to be analyzed, which is necessary to detect materials of very low density.
In concrete terms, XSpectra® analyses the interaction of x-ray photons at different energies, and compares the energy of the photons absorbed by the product and the various contaminants present in and on the surface of it, if this were present (because different materials absorb energy differently).
In just a few milliseconds it generates a chemical and physical analysis of every product on the production line, whether loose or packaged, and identifies the contaminants present.
The great revolution lies in the fact that, while most analysis systems can only find high-intensity materials such as metal, stone or glass, XSpectra® can also detect very low intensity contaminants such as nuts, insects, wood, and plastic.
Common examples of products rejected by XSpectra® include wood found in glass jars containing olives, pieces of nitrile gloves in chocolate bars, rubber bands inside tomato cans, pieces of carapace in filled pasta, and Pit and EPDM gasket fragments in sandwich bread.
