The pet population has increased on many continents during COVID-19, which has also been driven by social isolation and smart working. Add to this an increasingly informed public about food and ingredients, and we find ourselves in a situation where pet owners demand the best for their animal friends.
Ensuring safe and contamination-free products has always been the most important premise for the pet food industry. However, new trends in production are forcing greater flexibility, while complying with regulations and directives, in order to meet market demands. With its broad portfolio of weighing and inspection solutions, Minebea Intec offers the right solution to ensure greater development of their business.
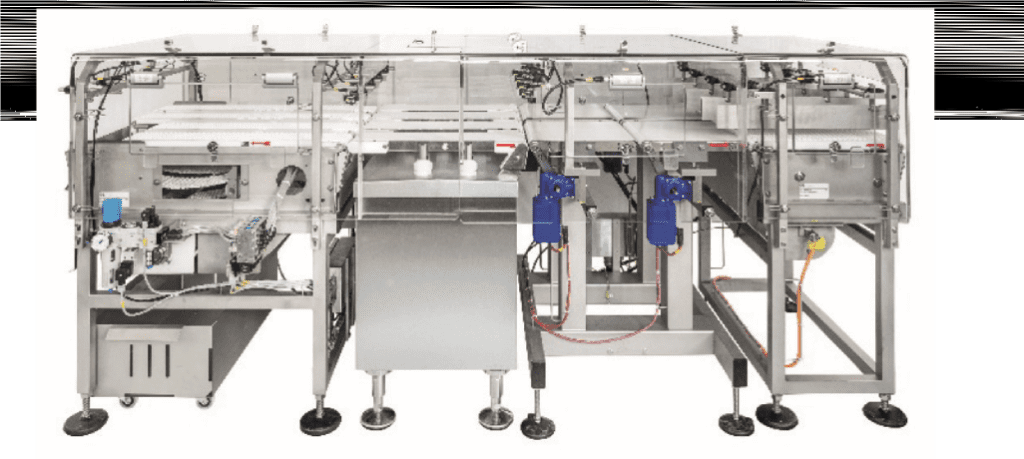
Pet food has long ceased to be just a source of sustenance; on the contrary, it often reflects the lifestyle of the family to which they belong. New topics such as sustainability or organic products, for example, are becoming increasingly important; these new foods are initially produced in smaller batches and for this purpose the machines used in the production line must be flexible and allow modifications even after initial installation.
The variety of foods on the market requires production lines to be increasingly versatile, with products taking on different formats: dry (kibble), wet (tins and sachets), semi-wet, fresh, dehydrated, freeze-dried, raw meat infused foods, treats and chewables. Slight variations in moisture within a product can be a common cause of high rejection levels; the reason being the increased conductivity level of the food when wet. The product effect is a problem that Minebea Intec metal detectors are able to address.
Minebea Intec meets highest requirements for foreign object detection
Over time, several new quality systems have been introduced for pet food production, such as HACCP, BRC, IFS, etc., many of which are the same as those used for human food. Metal detectors and X-ray inspection equipment are used at various critical control points in production to exclude contamination by foreign objects in metal, stone, plastic or other materials, and this starts already before processing, when the basic ingredients are examined before being processed.
During processing steps such as mixing ingredients, product contamination can be caused by rubbing containers or machines. At the end of the production chain, X-ray inspection systems are suitable not only for the final detection of foreign bodies, but also for checking completeness or filling level regardless of the type of packaging. Defective products and related recall campaigns can cause severe damage to the company’s image and financial losses; to avoid this, metal detectors and inspection devices are used that can be individually designed to meet legal requirements and production needs.
A number of pet food companies rely on Minebea Intec’s Vistus® metal detection systems to ensure that raw materials and finished products are unaffected by the presence of metals, regardless of whether they are inspected in the packaging line or one step earlier in the processing of ingredients. For pre-packaged products, the Vistus® can be mounted on existing and technically suitable conveyors or integrated as a stand-alone system. For non-packaged products, the Vistus® can alternatively be used as a free-falling unit, performing checks at the time of filling. Integration is not complicated and special product guide tubes are available as part of the Minebea Intec supply. In food processing, the use of Vistus® is widespread as part of a piping system. As with the free-fall application, integration is not complicated and special product guide pipes are available as part of the Minebea Intec supply.
Precise weighing eliminates product loss

In addition to checking for foreign objects, Minebea Intec checkweighers and load cells are ideal for maintaining the exact quantities of components in each recipe. When weighing packages containing products such as pet food, the Synus® checkweigher ensures that each individual package contains the correct amount of product and complies with average weight control regulations by weighing 100 per cent of the production.
If space in the production line is limited, we recommend the use of the Cosynus® combination device, a solution consisting of the Synus® checkweigher and the Vistus® metal detector: in this case, the user controls and configures two machines via a common interface, which is clear and time-saving.
Minebea Intec’s new range of Vision systems, including the VisioPointer®, provide substantial quality control. The multiple uses and configurations of this system include top, bottom and side cameras that allow packages and products to be inspected from any side.
Among the most common uses are checking labels, both for content and location, identifying contamination of seals and other packaging details.
www.minebea-intec.com